0
years of activity
0
employees
0
export market
0
million items produced per year
All benefits, no compromises
Replacing metal components with plastic ones represents the challenge for your future. And of our present.
Significantly Lower Costs
Our plastic molding solutions offer a cost-effective alternative to metal components, reducing material expenses, production costs, and overall operational expenditures.
Reduced Weight
Plastic components are significantly lighter than their metal counterparts, leading to easier handling, improved energy efficiency in transportation, and enhanced performance in various applications.
Metal-Like Strength and Durability
Engineered to meet demanding mechanical and structural requirements, our plastic parts provide exceptional strength, wear resistance, and longevity, making them a reliable substitute for metal.
High-Volume Production with Fast Turnaround
Advanced injection molding technology enables the mass production of high-quality components within short lead times, ensuring efficiency and scalability for your business.
Simplified Logistics and Supply Chain
Lightweight and easy to transport, plastic components simplify logistics, reduce shipping costs, and streamline supply chain operations compared to traditional metal parts.
Versatile and Highly Customizable Designs
Plastic molding allows for intricate geometries, complex shapes, and design flexibility, making it possible to create customized solutions tailored to specific industry needs.
Automation, Precision, and Efficiencyat Every Stage
Cutting-edge technology and smart automation for seamless production, maximum quality, and real-time monitoring.
Every day, over 34 automatic shuttles carry 2600 loads from production through to quality control and packing.
Because our workers can focus above all on activities with a high added value.
51 injection moulding machines for power of up to 850 tons and 11 Bi-material injection moulding machines.
Because we use the best possible technology to suit every need.
Every island is served by automatically controlled machines and an operator at the end of the line.
Achieving complete quality, even on mass produced pieces.
OEE monitored over 24h in real time for each island and transmitted to the various department screens.
To know what is happening in each department in a single glance.

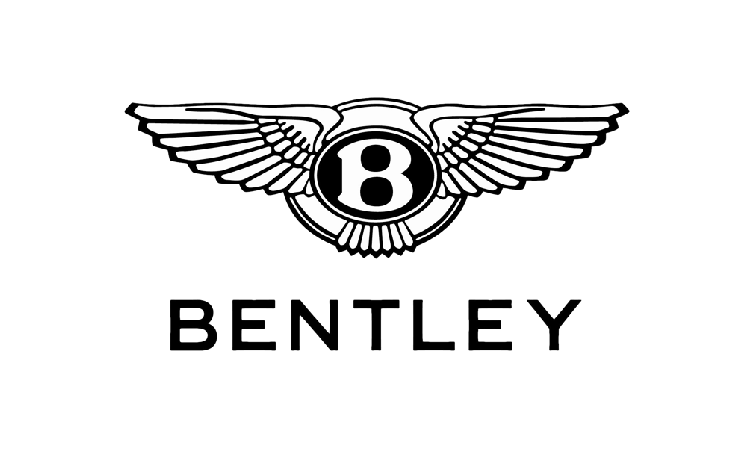
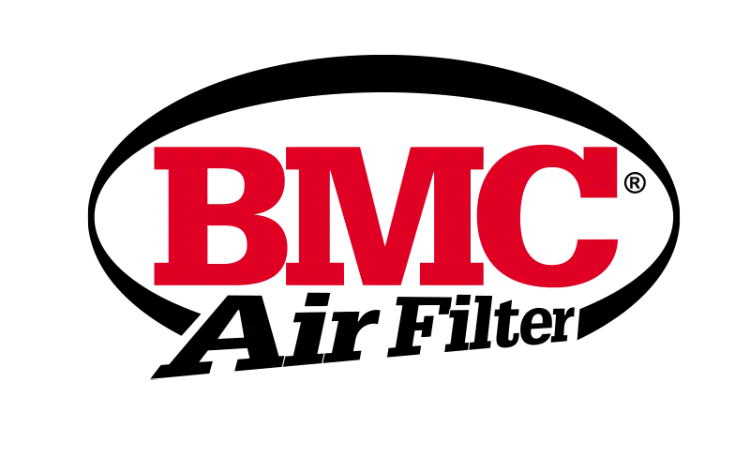
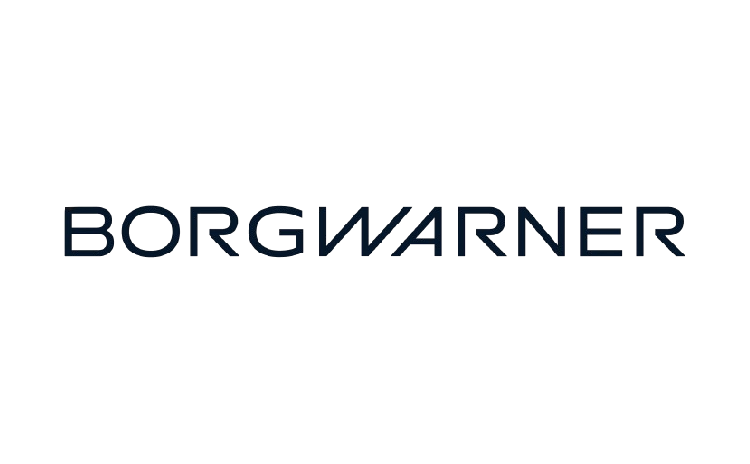
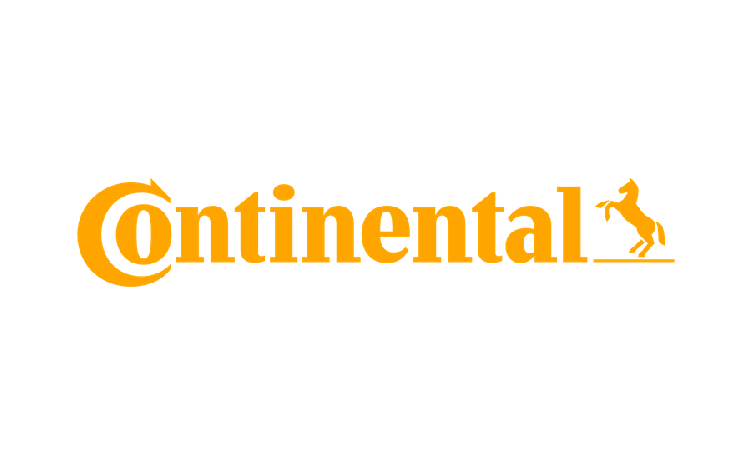
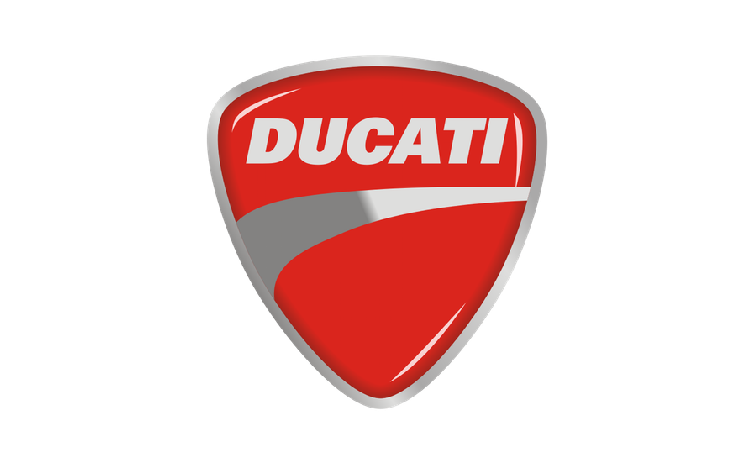
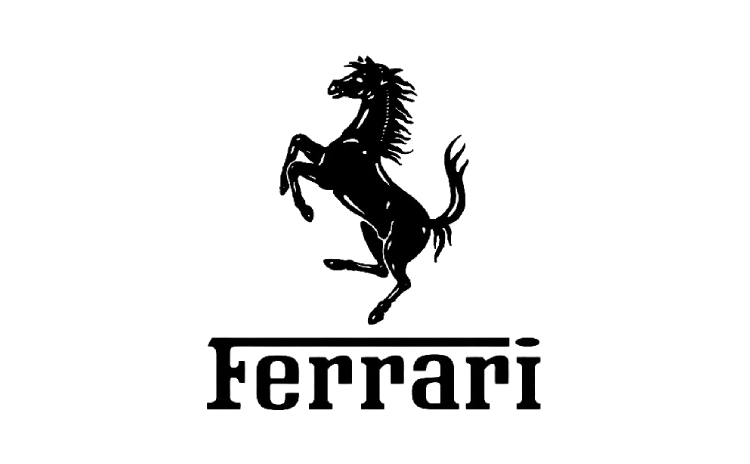

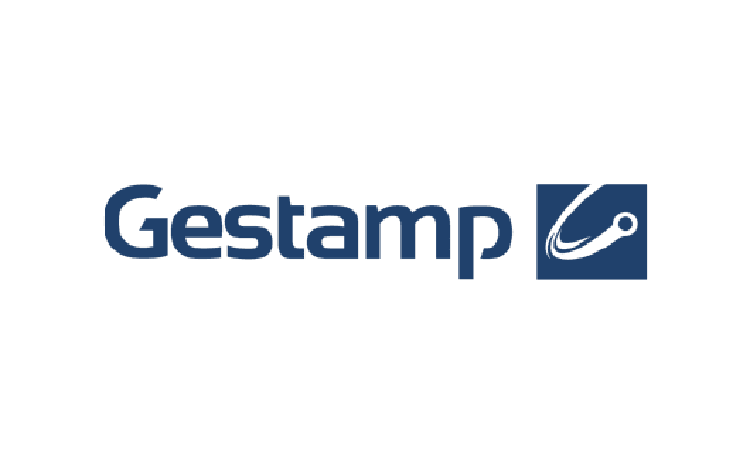
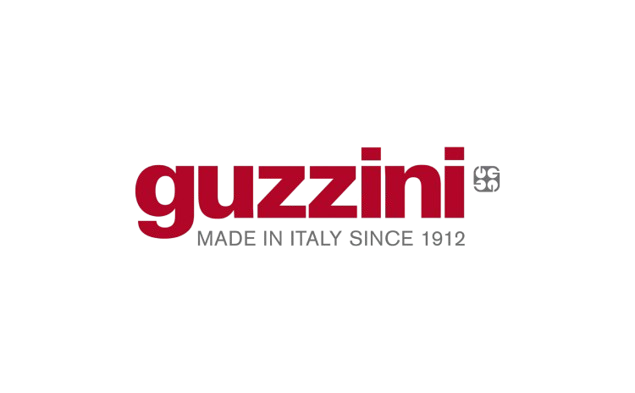
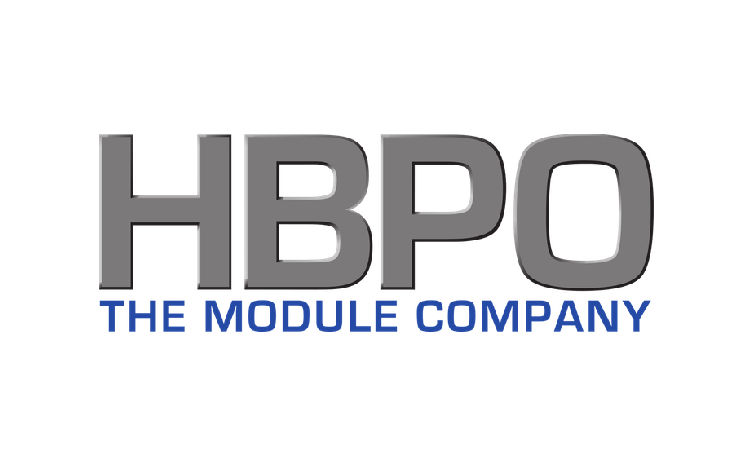
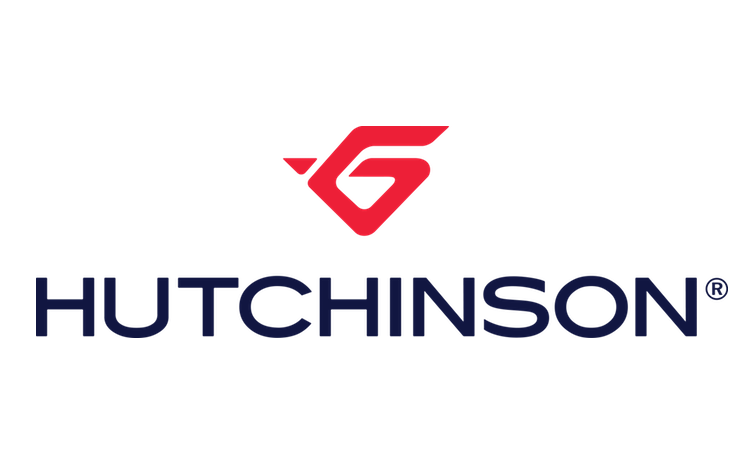
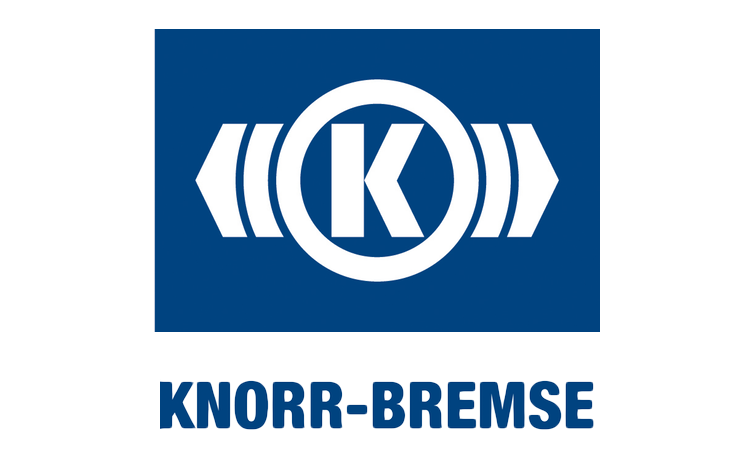

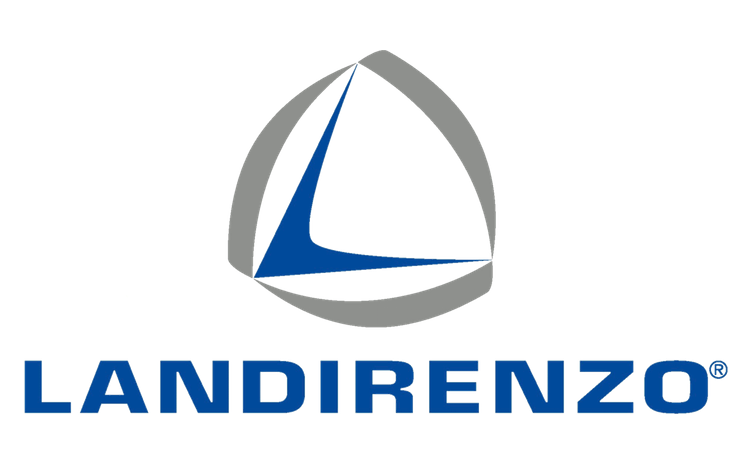
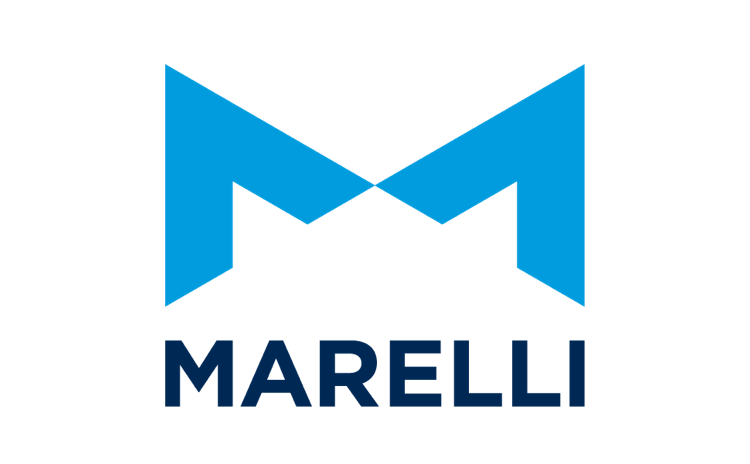
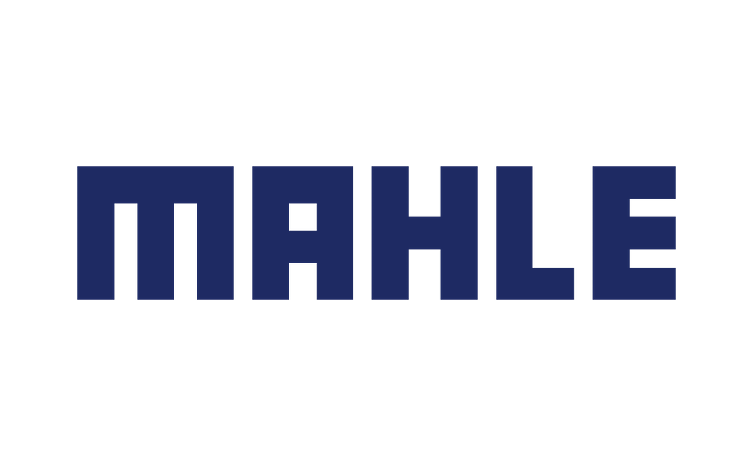
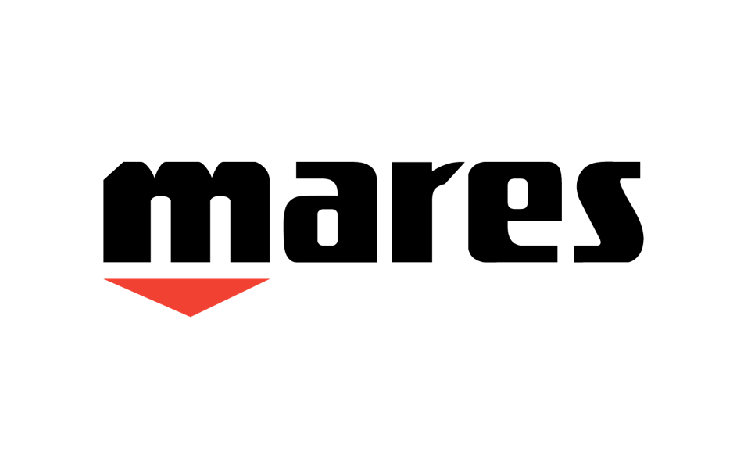
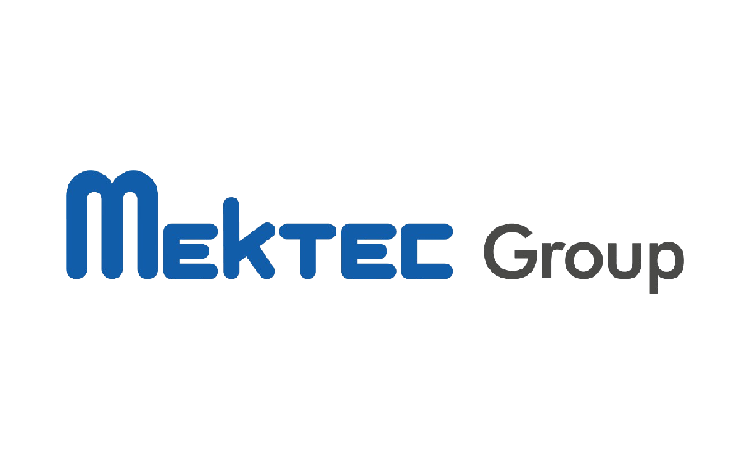

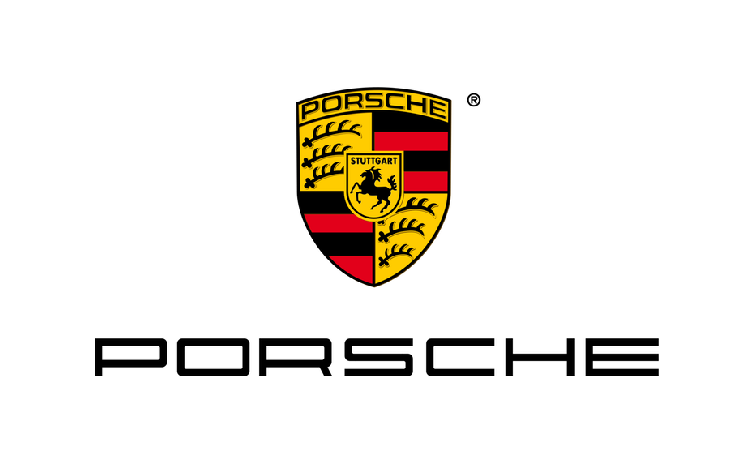
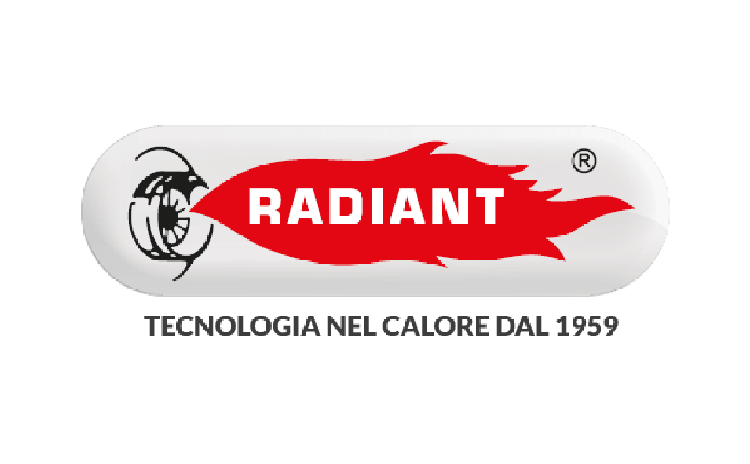
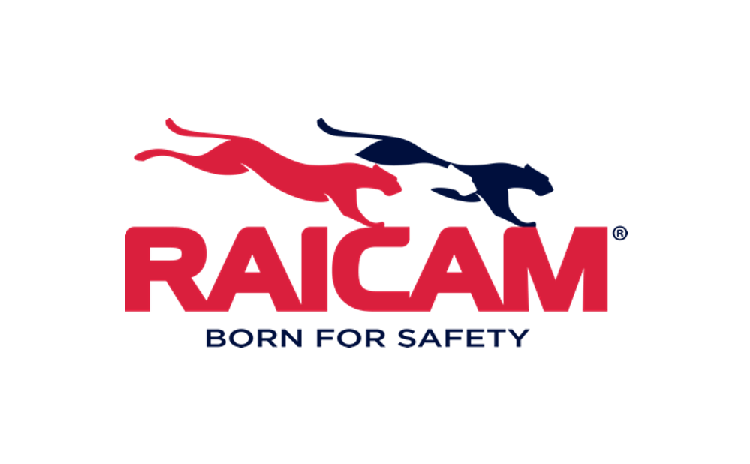
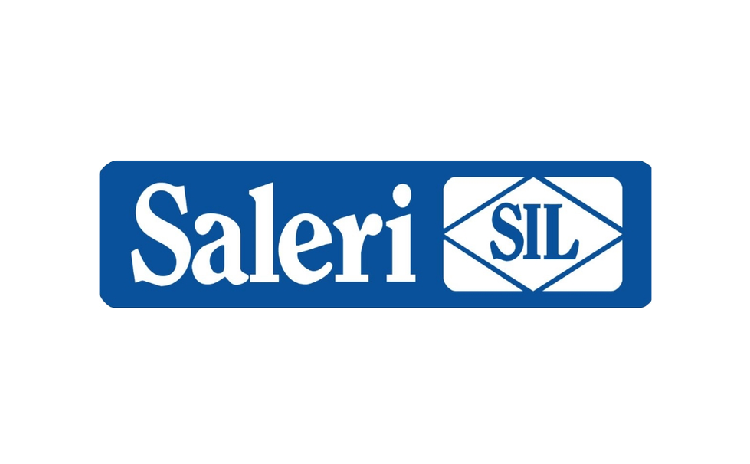

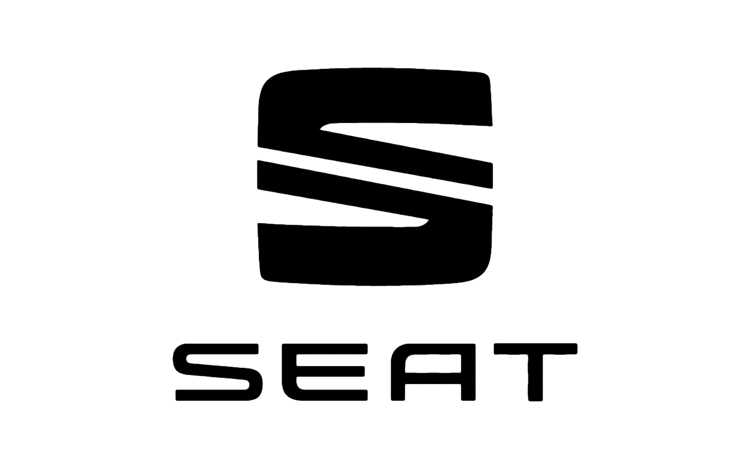
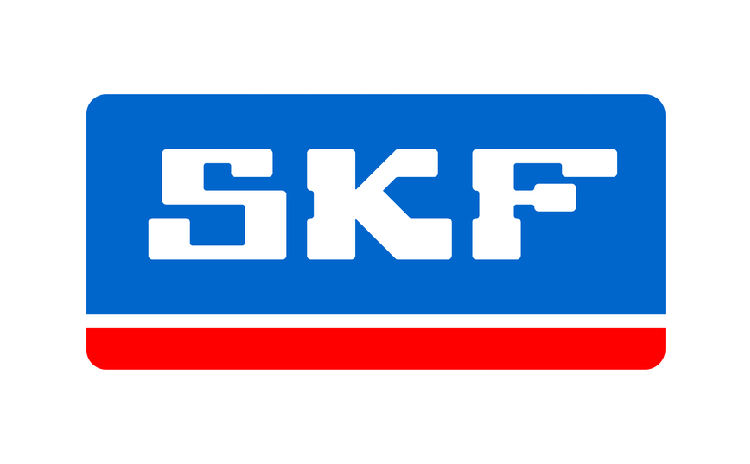
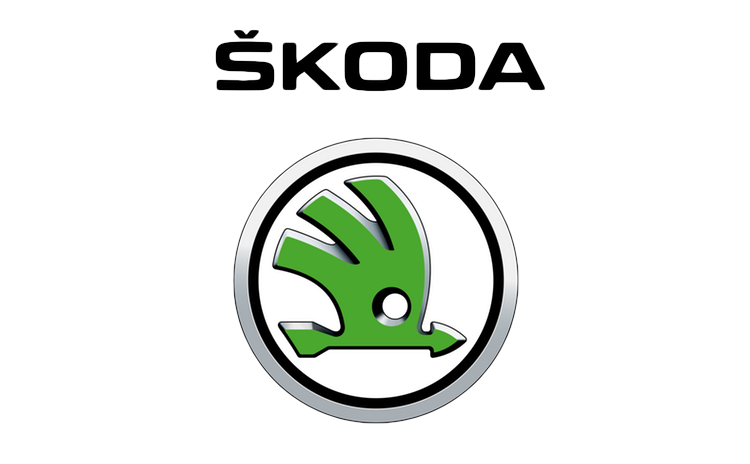
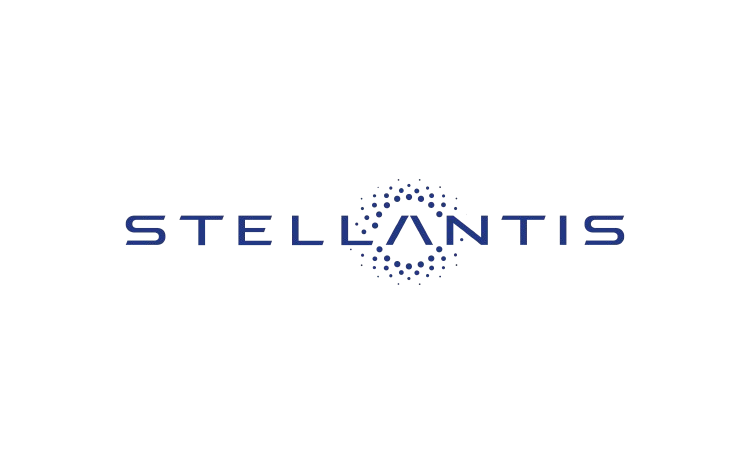

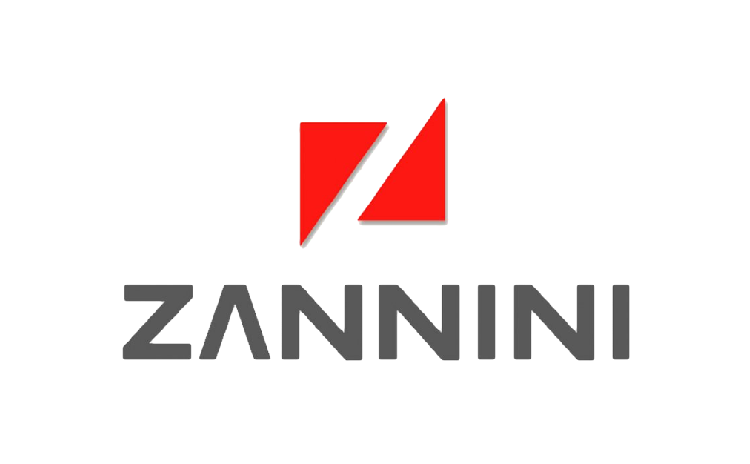
